Basics of Bending
When used in reference to stamping dies bending is a specific type of process. In the bending operation, the material is formed around a straight axis or an imaginary line, one could say. When talking about bending, one has to learn the vocabulary used to understand the process. Critical elements are the bend radius, bend lines and bend axes.
- The bend radius is tangent to the inner plane surface of the piece part.
- The bend lines occur at the tendency of the bend radius with the inner plane surface.
- The bend radius is perpendicular to the inner plane surface at the bend line.
- The bend axis is located at the center of the bend radius.
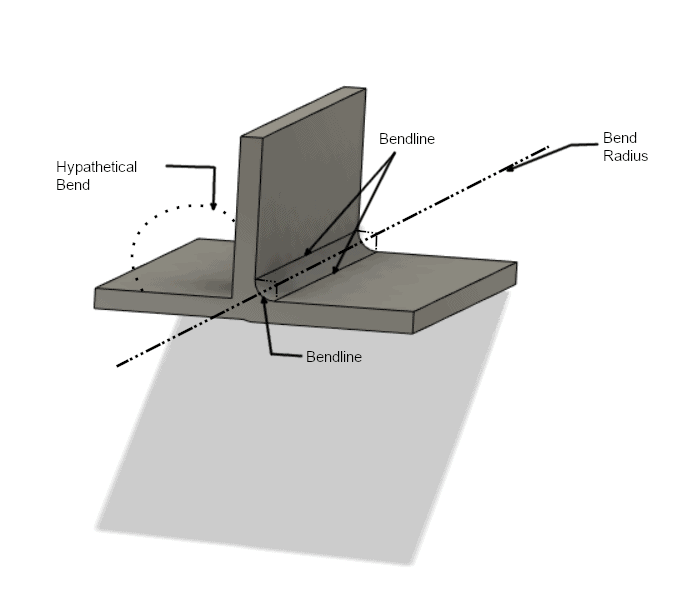
Bending stress
When we are tool making, it is good for us to have an understanding of the forces being applied to the material and how they react with the material. If we had a hypothetical bar of metal, as we apply bending force, causing the metal to deflect/bend on the inner and outer surfaces, the inner surface to the bend tends to get shorter and the outer surface tends to get longer. Somewhere in between the inner and outer surfaces, there is a neutral plane. Whenever we apply forces to a material that exceeds the material elastic limits, it causes plastics to flow within the bend area resulting in permanent deformation of the material.
( insert graphic showing plastic flow)
Bending is a type of forming operation that leads to the distortion of the metal and is called plastic deformation, which is associated with the plastic flow that takes place in the bend area.
This principle is important to understand because the main factors which determine bend aggressiveness or severity of the bend are stock material thickness, the severity of the bend angle, and size of the bend radius.
These factors affect the bend as follows:
- Increasing stock material thickness increases the aggressiveness of the bend
- Increasing the bend angle increases the severity
- Decreasing the bend radius increases the severity.
Keep in mind that softer material which is more ductile will tolerate more bending operations.
Bend allowance
The curved neutral plane of the bend areas is called the bend allowance. As a toolmaker, it is important to understand bend allowance and the factors affecting it, such as the bend angle. The length of the curve is directly in proportion to the size of the angle.
Bend Elements Summarized
Bend Axis– the bend axis is the neutral center of the bend radius, the bend axis is the straight-line axis around which the material is formed at the desired radius.
Bend radius– the bend radius is the inner arc of the bend and is tangent to the inner flat planes that would extend outward from the radius.
Bend line-there are only two bend lines associated with each bend, they are actually imaginary lines that run tangent to the bend radius.
Bend Angle– the bend angle is the included angle of the two most extreme points of the bend radius, originated from the bend axis. Just note that bend angle is not the included angle of the piece part.
Bend area– is the space included in the bend angle.
Inner surface – is on the shorter side of compression of the bend
Outer surface– is on the outer side of the bend and is stretched longer as a result of bending
Neutral plane– is an imaginary or theoretical plane originated from the bending stresses
Estimating Flat-Blank Length
To estimate the length of the workpiece we have to find the length of the theoretical neutral plan. To find the neutral plan, we first have to find the bend allowance for A for each bend then B is the length of the flat blank.
( insert drawing explaining equations)
B=L1+A+L2
To find A :
A=(R+C)2piN/360
Conclusion
This chapter in the text explained mostly the application of bending principles, but there is a lot more to it, including piercing a component after bending. As are most of the die build articles, this is a summary from the text of what I think is most pertinent to use in preparation for my C OF Q test to complete my tool and die apprenticeship. If you liked this article and want to know more about tool making and machining and skilled trades, in general, please subscribe to our email.